Power Meets Sustainability: The Rise of Electric Excavators in Mining
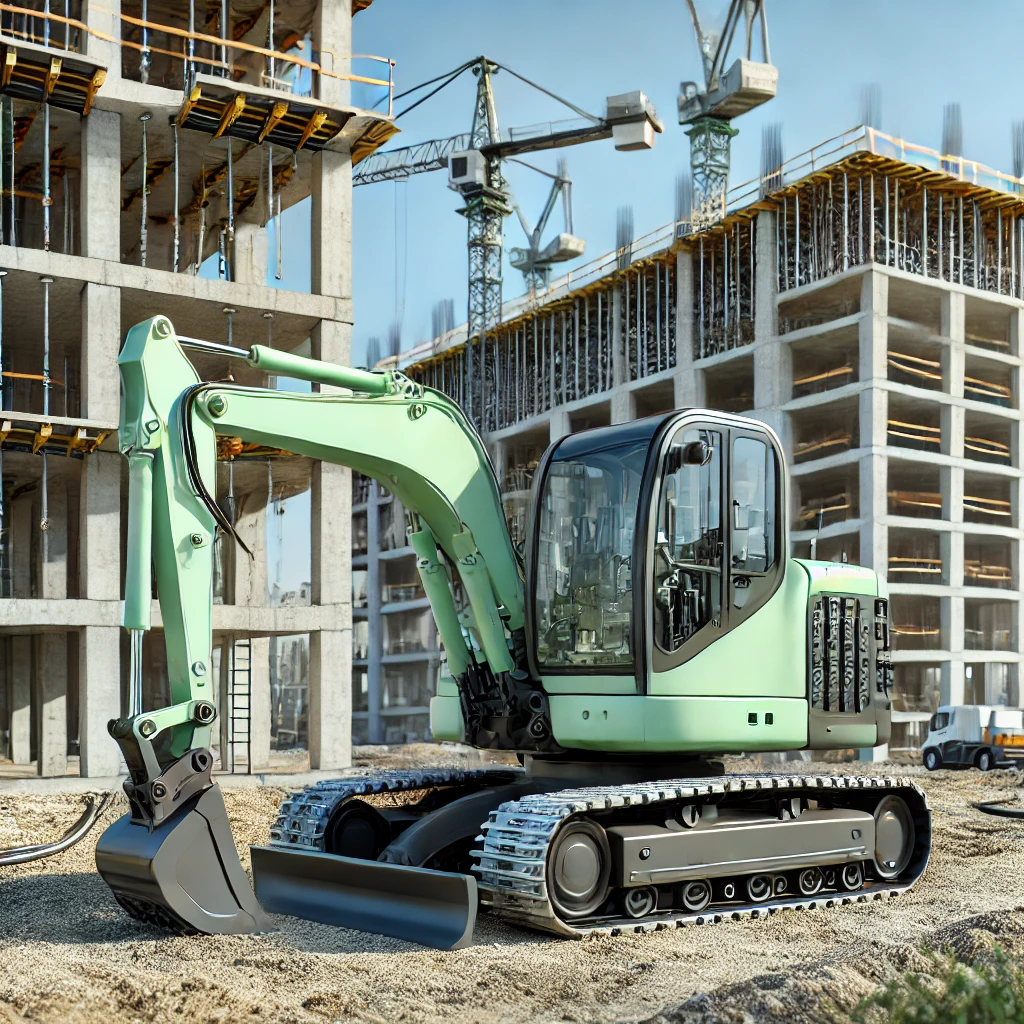
Imagine a world where mining operations are not only efficient but also gentle on the environment. With the introduction of the Komatsu PC4000-11E electric excavator, that world is inching closer to reality. This machine is not just another piece of construction equipment; it represents a significant leap toward sustainable practices in an industry often criticized for its environmental impact. As someone who grew up hearing about the heavy, polluting machines used in construction sites, the prospect of an electric excavator is not just exciting—it's revolutionary. Let's delve into what makes this excavator stand out and how it can reshape the future of mining.
Unpacking the Komatsu PC4000-11E
The Komatsu PC4000-11E marks a significant step in mining technology. This hydraulic mining excavator is not just about brute force; it symbolizes a shift to cleaner, more efficient operations. With an operating weight of 409 tons, it is built to tackle demanding jobs in the toughest environments. But what sets it apart from traditional diesel-driven equipment? Let’s explore.
Overview of Specifications
The PC4000-11E is designed specifically for the mining industry. Here’s a snapshot of its specs:
Model | Operating Weight | Emission Reduction |
---|---|---|
PC4000-11E | 409 tons | Up to 95% |
This machine is a remarkable combination of power and environmental responsibility. It weighs 400 tons, making it one of the heavier options on the market. However, its electric drive and battery technology push it ahead in emission performance. Achieving a reduction of up to 95% in emissions is no small feat, proving that mining can be both powerful and cleaner.
Comparison with Diesel-Driven Excavators
Traditionally, diesel-powered excavators have dominated the mining sector. They are known for their robust capabilities but come with substantial drawbacks. High fuel consumption and significant emissions contribute to environmental concerns. The PC4000-11E presents a solution. It offers the powerful digging force of standard diesel machines, while also boasting the operational benefits of electric systems.
- Efficiency: Users can expect up to 50% savings in total cost of ownership compared to diesel machines.
- Maintenance: The electric nature of the PC4000-11E simplifies machine control, leading to faster troubleshooting and lower maintenance costs.
- Environmental Impact: The drastic reduction in emissions sets a new standard for the industry.
How does a machine that weighs 409 tons effectively achieve these advantages? The answer lies in its intelligent design and innovative features. The system is built to work with Komatsu’s Trolley Truck Assist System for enhanced performance, specifically in mining operations. This synergy allows for longer operational hours at a lower energy cost.
Innovative Technology Features
Komatsu is not just about digging deep. They’ve embraced smart technology to improve performance. The fully automatic cable drum in the PC4000-11E makes operations run more smoothly. It simplifies maneuvering, saving precious time in bustling work environments.
Moreover, the electrical system's design allows for quick troubleshooting. This contributes to the overall availability of the machine. In mining, every minute counts. Thus, having a machine that is easier to maintain can make a substantial difference.
"This is the future of mining equipment—powerful but cleaner." - Peter Buhles
Target Applications in Mining Operations
The Komatsu PC4000-11E is specifically crafted for various applications in mining. Its versatility makes it suitable for:
- Open-pit mining operations
- Quarrying
- Heavy excavation tasks
- Applications where environmental standards are paramount
In pilot programs, customers using this excavator have achieved a 47% reduction in total cost of ownership. That's impressive! This figure highlights a move towards sustainable operations, without sacrificing power and performance.
Overall, the Komatsu PC4000-11E showcases what the future of mining equipment looks like. By integrating traditional power with innovative technology, it's setting a new benchmark for the industry. As we delve deeper into its features, we can see that sustainability and efficiency go hand in hand in the modern world.
The Economics of Electric Excavators: A Financial Perspective
The construction industry is evolving. Transitioning from traditional diesel machinery to electric excavators presents significant financial advantages. Operators and fleet managers are turning their attention to the potential cost savings that electric machinery can offer.
Cost-saving Potential of Using Electric Machinery
Why should companies consider electric excavators? The answer lies in the economics. First and foremost, electric machinery can significantly reduce operational costs.
- Fuel costs are lower. Electric power tends to be less expensive than diesel.
- Maintenance expenses are also reduced. Electric machines have fewer moving parts, which means less wear and tear.
- Emission regulations are getting stricter. Companies can avoid hefty fines while maintaining their green credentials.
According to industry data, electric excavators can achieve a 50% reduction in operational costs compared to their diesel counterparts. As an industry analyst aptly states,
“A 50% reduction in operational costs is a game changer for fleet managers.”It's clear that the shift to electric technology can have profound financial implications.
Comparison of Total Cost of Ownership with Conventional Machines
Examining the Total Cost of Ownership (TCO) is vital when deciding between electric and diesel excavators. The TCO includes purchase price, fuel costs, maintenance, and any potential fines or fees.
Interestingly, studies indicate that electric excavators demonstrate a 47% savings in TCO based on real-world pilot programs. This is not mere speculation but backed by solid data.
Type of Excavator | Total Cost of Ownership Savings |
---|---|
Electric Excavator | 50% |
Pilot Study Findings | 47% |
Real-World Pilot Study Findings and Customer Experiences
Studies involving the new Komatsu PC4000-11E hydraulic excavator showcase how real-world customers have benefited. These excavators offer the digging force of traditional machines while being emission-free. Users in pilot programs reported substantial savings.
This aligns with Komatsu's claim that its excavator can provide a 50% savings in TCO . However, it’s essential to note that these numbers can vary based on individual operational circumstances.
Understanding Fuel and Maintenance Cost Fluctuations
Fluctuations in fuel costs can heavily affect operational expenses. For example, if diesel prices rise, electrical machines become even more financially attractive. Electric prices do not face the same volatility as traditional fuels.
Additionally, with electric machinery requiring less maintenance, companies can expect lower downtime and higher productivity. An electric excavator can operate 24/7 with fewer interruptions for repairs and fuel refills.
As companies make the shift to electric, better planning of operation scenarios can lead to maximized savings. Fleet managers can utilize energy cost fluctuations to their advantage. It’s a compelling way for operations to protect their bottom line.
Conclusion
While this section does not conclude the overall discussion, one key takeaway rings loud: the financial benefits of electric excavators are hard to ignore. With real-world data proving significant cost savings, the future of mobile machinery seems bright and green.
The economics paint a clear picture: electric excavators are not just a passing trend — they represent a smarter choice for the future of the construction industry.
Industry Implications of Electric Equipment
Shift Towards Sustainability in Heavy Machinery
The mining industry is witnessing a significant transformation, moving towards sustainable practices. This shift is vital for reducing the environmental impact of heavy machinery. Sustainability refers to the ability to meet present needs without compromising future generations.
Many companies are adopting electric machinery. Why? It promises lower emissions and reduced operational costs. For instance, the new Komatsu PC4000-11E electric excavator can cut emissions by up to 95%. Imagine what this means for the environment and operational expenses!
Challenges and Opportunities for Traditional Miners
Yet, this transition comes with its challenges. Traditional miners may face difficulties adapting to new technologies. The initial investment is significant. However, the long-term savings can be substantial, offering a new lease on operational efficiency.
- Challenges:
- High setup costs for electric equipment.
- Need for training on new systems and technologies.
- Opportunities:
- Access to government incentives for sustainable practices.
- Improved public perception leading to brand loyalty.
Potential Regulatory Impacts and Incentives for Electric Adoption
Regulatory changes are also shaping the landscape. Governments are increasingly promoting green technologies through incentives, tax breaks, and support programs. These policies aim to foster a transition to electric equipment.
The regulatory framework is evolving as awareness of climate issues grows. Companies investing in sustainable machinery may benefit from fewer regulations and more government backing. But what happens if you don’t adapt?
Those who lag behind may face fines and costly retrofits. Staying ahead of regulations is crucial for maintaining an edge in the competitive mining sector.
Feedback from Operators and Industry Leaders
Feedback from industry leaders adds depth to this discussion. A mining executive once stated,
“This shift is not just a trend; it's the new normal for mining operations.”This sentiment reflects a profound understanding of the industry’s trajectory. As electric equipment becomes the standard, operators report better efficiency and lower expenses.
Committing to sustainable practices is more than a business decision; it’s a moral imperative. Today’s operators view their machinery as not just tools but as partners in their quest for innovation.
Historical Context and Future Predictions
Understanding the historical evolution of mining equipment is crucial. In previous decades, diesel-heavy machinery ruled the market. However, as technology advanced, the drawbacks of traditional machinery became evident. Now, we stand on the cusp of a new era.
Future predictions indicate a strong inclination towards electric machinery. A recent study showed that over 70% of mining firms are planning to adopt electric models within the next three to five years. This is a clear indicator of the industry's movement.
Data Trends in Electric Adoption
Year | Percentage of Firms Adopting Electric Models |
---|---|
2023 | 30% |
2025 | 55% |
2027 | 70% |
With the ongoing advancements in electric technology, the mining industry is positioned to thrive sustainably. We see ourselves as partners to our customers, supporting and collaborating with them on their journey toward a more sustainable and efficient mining operation.
As more companies embrace this new normal, we can expect to see not just economic benefits but also a substantial positive impact on our planet. Will this industry evolution lead to a greener future? Only time will tell.
Navigating the Transition: Insights from Experts
Expert Opinions on the Future of Mining and Machinery
As the mining industry evolves, many experts are sharing their insights on the future prospects of mining and machinery. They highlight the trend towards electrification. Why? Because it offers both cost savings and environmental benefits .
According to various industry leaders, the transition to electric machinery is not just a passing trend. It represents a fundamental shift in how companies operate. Peter Buhles, Vice President of Sales and Service at Komatsu, explains, “We see ourselves as partners to our customers, supporting and collaborating with them on their journey toward a more sustainable and efficient mining operation.”
Case Studies from Companies Adopting Electric Machinery
Several companies have begun adopting electric machinery with remarkable results. For example, Komatsu's new PC4000-11E hydraulic mining excavator combines high performance with reduced emissions. Data shows that customers in pilot programs have seen a 47% savings in total cost of ownership. This is a substantial amount in any business.
- Performance: The electric excavators are designed to operate efficiently in demanding environments.
- Emissions: They can reduce emissions by up to 95% .
- Maintenance: The simpler control system helps with quicker troubleshooting.
Such case studies illustrate the real potential of electric machinery within the industry. As companies switch over, they are not only reaping financial rewards but also creating a cleaner working environment.
Training and Readiness for Operators
But, it’s not just about the machinery. There’s an important element of training . New operators must be ready to handle these advanced machines. Training modules for electric excavator operations have been developed to help ease this transition.
“
Proper training is essential for the successful adoption of electric excavation equipment.” - Training Coordinator.
This quote highlights that ensuring operators are ready is key. Training includes:
- Real-world simulations.
- Safety protocols specific to electric machinery.
- Operational efficiency techniques.
Balancing Performance and Environmental Impact
The balance between performance and sustainability is crucial. How do mining companies maintain efficiency while reducing their carbon footprint? The answer lies in innovative technology like the Komatsu Trolley Truck Assist System. When paired with electric machines, it creates a synergistic effect that maximizes output while minimizing harm to the environment.
Companies are recognizing that environmental responsibility is not just a trend but an essential component of their operational strategy. Meeting compliance regulations while increasing productivity can seem challenging, but advancements in electric machinery make it possible.
Monitoring Progress: Data and Feedback
Consider the following data reflecting the transition to electric equipment:
Metric | Percentage |
---|---|
Training Completion Rates Among Operators | 85% |
Feedback on New Machinery Performance | 90% Positive |
This data indicates that both operators and employers are adapting well to these changes. Progress is being made on multiple fronts. Companies can feel confident about embracing this shift.
As we build on these trends, the conversations and adjustments will continue. The mining industry is undoubtedly on a path towards greater sustainability and efficiency. The journey may have challenges. But with expert insights and case studies guiding the way, success is within reach.
The Path Forward: Why Electric is the Way of the Future
Conclusion: Advantages of Electric Excavators
Electric excavators represent a significant leap forward in heavy equipment operation. They combine efficiency, performance, and environmental consciousness. Imagine a powerful excavator that not only completes tasks effectively but also contributes to a cleaner environment. This is what electric excavators deliver.
- Reduced Emissions: Electric excavators can cut emissions by up to 95%. This is a game-changer in the mining sector where air quality is often compromised.
- Lower Operating Costs: Komatsu's latest model, the PC4000-11E , has shown a remarkable 47% reduction in total cost of ownership in pilot programs. Less fuel means more savings.
- Improved Efficiency: The automatic cable drum of electric excavators simplifies operation. This saves time and enhances overall productivity.
Final Thoughts on Sustainability and Mining
The mining industry is under increasing pressure to become more sustainable. As global awareness of climate change grows, the demand for cleaner operations intensifies. Electric excavators align perfectly with this trend.
By integrating electric technology, companies are actively contributing to a sustainable future. This shift not only mitigates environmental impact but also promotes responsible resource management. It’s an opportunity to rethink outdated practices and embrace innovation.
Call to Action for Industry Engagement
It is imperative for industry leaders, policymakers, and stakeholders to come together. Engagement can foster the growth of electric heavy equipment. Collaboration will enhance the transition to sustainable practices in mining.
Organizations should invest in technology, training, and research. They must also collaborate to share insights and best practices. The shift to electric machinery isn’t just beneficial—it’s essential.
As the Environmental Advocate states,
“Embracing electric technology will be crucial for our industry's future.”
Looking Ahead: What’s Next for Electric Heavy Equipment
The future of electric heavy equipment looks promising. There are several key innovations on the horizon:
- Battery Technology: Ongoing advancements in battery tech are needed. This will enhance capacity and reduce charge times.
- Integration with Renewable Energy: Pairing electric equipment with solar or wind can further decrease environmental impacts.
- Smart Technologies: Incorporating IoT and AI into electric heavy machinery will optimize operations and improve safety measures.
As electric heavy equipment becomes more prevalent, we must remain adaptable and proactive. The mining industry stands at a crossroads. Will it embrace change and lead in sustainability?
In conclusion, electric excavators offer a compelling path forward for both sustainability and operational efficiency in mining. They signify a necessary shift towards environmentally responsible practices that will define the future of the industry. The time to act is now.
TL;DR: Electric excavators are environmentally friendly and cost-effective, offering emission reductions of up to 95% and significant cost savings. The industry must engage in sustainability initiatives to embrace electric technology, paving the way for a greener future in mining.